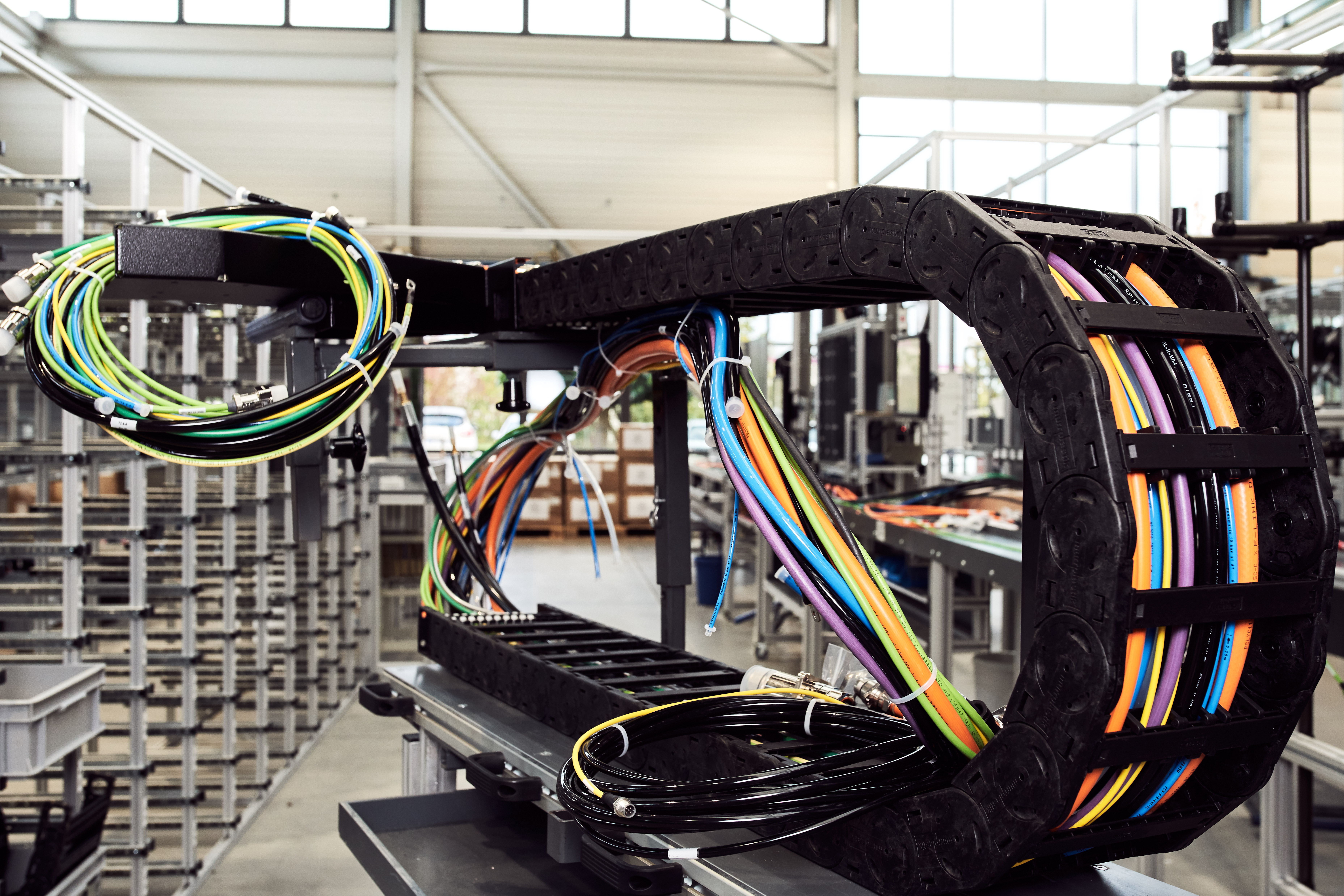
Changes are systematically implemented and seamlessly documented
Changes, modifications, corrections, further developments and new designs are part and parcel of everyday operations in the mechanical and plant engineering sector. As a systems supplier in the installation technology field, the LQ Group has to deal with a large number of changes every day. Since the company was founded, LQ has operated its own change management process so that they always maintain an overview and ensure that all changes are incorporated at the time requested.
Manufacturing companies today have to operate in a dynamic environment. This, combined with increased competitive pressures, brings changes every day, impacting both products and the production processes. According to the Institute for Machine Tools and Industrial Management at the Technical University of Munich more than half of the companies surveyed make a change to the production process more frequently than once every three days. Furthermore, a good two-thirds of manufacturing companies have to deal with over a hundred changes in production every year.
The significance of changes to products and in production is steadily increasing. Experts agree that this is an area that will become even more important in the future. Systematic and traceable change management is not only a significant challenge for companies: it is also a crucial factor for ensuring that the company remains competitive over the long term.
Considerable experience with change management
As a systems supplier, the LQ Group is involved in all the customers’ changes and adjustments. Consequently, an effective change management system has been part of LQ's day-to-day routine since the company was founded. In 2023 alone, LQ implemented over 3,000 changes. At a practical level, this means that changes actually have to be implemented and documented every day.
There are many reasons for the frequent changes and adjustments. These are not only changes to products or product innovations. Other reasons include changes to materials and articles, drawing changes from customers, discontinuation of articles by the manufacturer, variations in the lengths of made-up cables or reconfiguration of assemblies. Other triggers are change requests in respect of parts lists from LQ's production and missing documents at LQ.
If a component is not available for a machine or if it has been exchanged, even if it only involves a tiny adjustment to the cable make-up, this has implications for the parts list and the price calculation. These changes to the part must also be taken into account in the purchasing, development and production departments. Most adjustments are needed during the development of new plant and machinery or when components are discontinued. It is always true that any work with customer-specific systems involves many changes.
A platform for all departments
With such a large number of changes, without a coordinated system there is always the risk of losing track or the relevant departments may get confused when it comes to processing the changes in the right order. At LQ the ERP system ensures that all changes are correct and are fully implemented on schedule and in all the relevant departments.
Change requests received from customers are processed in LQ’s change management department. This involves first filtering all relevant elements of the customers’ change numbers. The new parts list is then run through LQ’s ERP system as part of an automated process and made available to all the relevant departments in real time. At the same time, an electronic folder is created and used to circulate the changes around the company. The folder contains all information such as emails, parts lists, change history and itemised lists. This informs all the relevant departments about the change, including the deadlines for processing.
Every step can be traced at any time
The seamless documentation ensures that the current status and the outstanding work steps can be traced at any time and can be accessed directly in the event of complaints or enquiries. All this ensures that adjustments are implemented without any problems, even if they need to be put in place on the same day. Manufacturing orders can be aligned immediately, if necessary. If new articles are involved, the purchasing department can obtain price quotations in a timely manner.
Summary
LQ has practised change management ever since the company was founded. The company's own in-house ERP system is used to record, communicate and document the changes. An electronic folder ensures that all necessary steps are carried out and documented so that they are traceable. The systems supplier's smooth change management gives customers the assurance that all pending changes are implemented in a controlled and consistent manner.