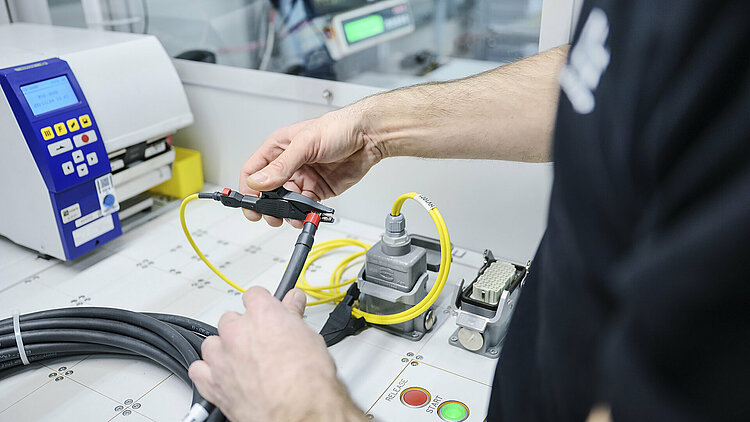
Zero defect strategy guarantees success
Products with especially high quality standards are – alongside factors such as a high degree of customer satisfaction, punctual delivery and flexibility – an important cornerstone in LQ Group's success. To ensure the best possible quality the company has adopted a zero defect strategy. “Made by LQ” quality has resulted in products achieving maximum reliability, even for demanding automation applications.
For the LQ Group making sure quality is as good as it can be is a crucial factor for ensuring that its products are reliable and function efficiently. So that possible faults can be ruled out right from the start, a zero defect strategy when manufacturing control and installation technology and the associated ongoing desire to make improvements are of key importance. Within the LQ Group it plays a key role in quality assurance and the Continuous Improvement Process (CIP). Here are the key points and elements:
Clear objective
Free of defects: The primary objective of a zero defect strategy is to produce goods and services that are free of any defects. Not only are defects not tolerated but proactive measures are taken to avoid them.
Customer satisfaction: Customers are more satisfied if defects are kept to a minimum, because the products and services are of the highest quality standards, which is what customers also expect from LQ.
Optimised processes
Systematic analysis: Processes are continuously monitored and analysed in order to identify vulnerabilities and potential sources of defects.
Standardisation: LQ develops and implements clear standards and processes in order to ensure that every step in the production process can be traced and carried out free of defects.
Employees who are trained and alert
Training for employees: Employees receive regular training on quality assurance, error prevention and the significance of the strategy.
Responsibility as part of the culture: LQ demands a culture within the company where every employee accepts responsibility for the quality of their work.
Preventive measures
Error avoidance: Instead of rectifying errors after they have occurred, the focus is on preventive measures so errors are avoided before they occur.
Continuous improvement: Feedback loops and continuous learning are implemented so that processes are successively improved.
Active quality management
Certifications: LQ uses recognised quality management systems such as a QM system in accordance with DIN ISO 9001:2015 in order to guarantee that quality standards are maintained.
Documentation: All processes and procedures are carefully documented so that deviations can be followed up and analysed and corrective measures initiated.
Continuous monitoring of outcomes
Figures and KPIs: Relevant figures such as the defect rate and punctuality are defined and monitored so that the success of the zero error strategy can be measured.
Feedback and audits: Regular audits and internal reviews ensure that the strategies for continuous quality assurance are implemented effectively and potential for improvement is identified.
Summary
The LQ Group's zero defect strategy aims to maximise quality and efficiency in all parts of the company. Through the combination of preventive measures, employee training and continuous process optimisation the LQ Group pursues the aim of eliminating defects and thus increasing customer satisfaction at the same time. Implementation of this strategy requires committed participation of all employees and the creation of a corporate culture that focuses on quality.