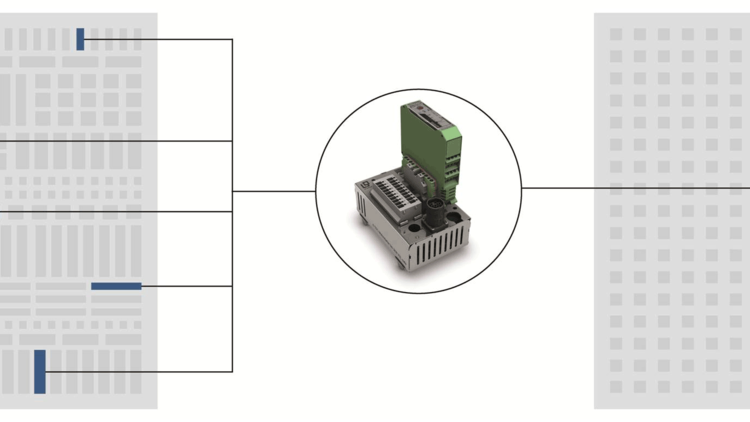
LQ mechatronic systems: Leading the way in the fight against the shortage of skilled labour
German engineers have a good reputation worldwide. Because the number of skilled workers in Germany continues to fall (in electrical engineering there is a shortage in 50 percent of professions) solutions must be found to balance this out – even without additional staff. Function modules instead of individual components are the key to success or, to put it in a nutshell, the modular switchgear cabinet. According to LQ mechatronic systems from Besigheim, modularisation of individual functions frees up unexpected reserves.
LQ does not produce any skilled labour but with its modular technology it ensures that the available potential can be put to better use. There is potential for savings throughout the entire production process, from development and design right through to assembly. Advantages can also be gained in relation to service. Whereas machine documentation and parts lists have been very expensive in terms of engineers’ time during development and design, the use of module solutions is significant for assembly, as it reduces the workload of skilled electricians.
The mechatronics experts at LQ have paid particular attention to documentation for machine tools and established that this ties up the valuable time of skilled employees. This is because accurate documentation has to be produced for each single strand, every connection to the machine and each individual component. The time and manpower required to handle many individual material numbers as well as to produce parts lists, drawings and circuit diagrams using conventional methods are considerable and the burden primarily falls on electrical engineers and technicians. However, consolidation of individual components into function modules frees up resources in the development department. The integration of CAD data in E-CAD and M-CAD programs such as E3, ePLAN and SolidWorks or Solid Edge simplify and shorten the process.
System suppliers such as LQ deliver complete functions instead of many individual parts. Modules are delivered to customers labelled, checked and ready for installation. A fitter can hang the module in the switchgear cabinet using the plug-and-play principle. An electrician is only required to check and commission the machine. By adopting this method, valuable assembly time is saved during this phase of machine design and the proportion of skilled manpower is substantially reduced.
Customers therefore delegate to a partner functions that are important but not their primary focus and the customers’ own skilled employees can concentrate on their core business – the further development of their machines. Even if a fault is found in the modular switchgear cabinet or when retrofitting new electrical components, there is no need to have a specialist on site, because the relevant software provides the diagnosis and the service engineer knows what has to be done. Last but not least, another point in favour of modularisation is the reduction in the effort required to support suppliers. This is because modularisation means fewer parts and therefore fewer suppliers who have to be coordinated. Improved process reliability is an additional benefit for machine manufacturers of concentrating on their core business and transferring the responsibility for complete components to systems suppliers.