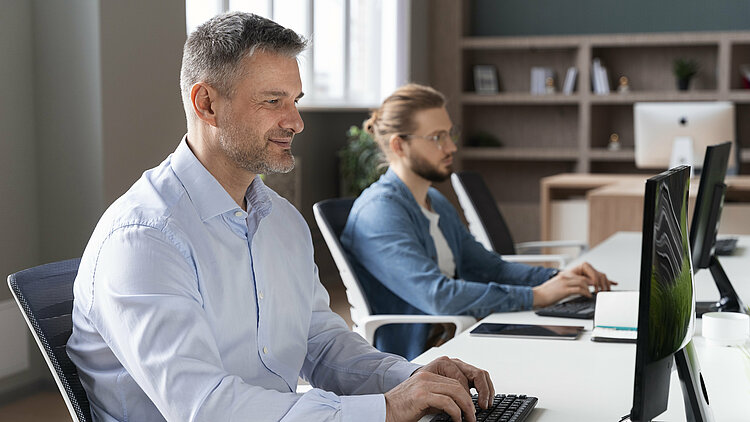
With added value since day 1
The LQ Group was already aware of the usefulness and importance of an ERP system when it was founded in 1999 and has been using its advantages consistently and successfully for a quarter of a century. Although mature and proven in exchanges with customers, new requirements and challenges bring with them the further development of the ERP system.
ERP systems (Enterprise Resource Planning systems) are nowadays an indispensable backbone for companies in the automation industry. In 1999, the year the LQ Group was founded, things looked very different. At that time, data such as material master data, production data, financial accounting data etc. was still entered manually into Excel lists in many places, which was time-consuming and sometimes error-prone. Not so at LQ. Even back then, those responsible showed foresight and used an ERP system right from the start.
ERP system offers many advantages
An ERP system is known to be a standard software for handling company processes with IT support. The focus is traditionally on business processes. This was also the case in the early years at LQ. However, production, sales and HR processes have also been supported for many years. There are also business intelligence components for reporting and evaluations.
LQ's ERP system not only supports standardized company processes, it also offers the additional advantage that all relevant company data is available in a database that can be accessed by all processes in real time. This implements the “single source of data” principle and avoids inconsistencies caused by redundant data. All LQ employees involved therefore have the same view of data and ongoing processes, such as orders, in real time. In addition, the company can prove the correctness of processes to the auditor much more easily. The issues of data security, access protection and reliability are also made easier by such a centralized system.
Start with core business management functions
Right from the start, LQ has relied on the module-based ERP software Avista, which makes it possible to combine standard and individual software. It was launched a quarter of a century ago with the core business functions of accounting, controlling, order processing and materials management. The functional scope of the ERP system has been continuously optimized and expanded over the years. In addition, further support for production was added in several stages through the independent and self-developed production planning system LQ PP. LQ PP is linked to the ERP system via standardized interfaces and thus integrated into the company processes. Most recently, the Avista system was expanded to include a planning module for customer planning.
A core element of the ERP system from LQ is the end-to-end support of order processing for customers. Order processing is fully implemented in the ERP system, from the order to production orders, dispatch and invoicing. All departments involved therefore have all the necessary information at a glance and know the current order status. The orders and customer planning form the basis for automatic scheduling runs, which make order proposals for material to the planners, which then only need to be triggered.
Connection of third parties via EDI interfaces
Thanks to end-to-end process support and a uniform, consistent database, all process participants can work together effectively regardless of departmental boundaries. Customers and suppliers can be connected to the Avista system via so-called EDI interfaces (Electronic Data Interface). Such EDI interfaces have been implemented with two customers. The ordering process and invoice dispatch were automated as a result. The result was a significant increase in efficiency. If required, further customers can be connected in this way.
The realization of an EDI interface requires a certain amount of effort, as it involves coordination and, if necessary, implementation services. The technical interface and data formats must be coordinated in advance of such an implementation, as EDI allows for several variants. Implementation on the supplier side has not been necessary to date, as the orders from LQ are usually transferred automatically to the suppliers in this case.
As described, interaction with third-party ERP systems takes place via EDI interfaces. If these are not available, this is done via Microsoft Office products that fulfill defined formats. The defined formats are implemented in Avista, which then enables data to be generated, sent and received automatically.
Mature and proven
Having been in use for over two decades, the ERP system from LQ is mature and proven. However, there are still modules that are not being used and one or two extensions are still required. As part of the company's LQ 5.0 digitalization programme, measures to optimise processes and provide even better IT support have been developed and are currently being implemented. In this context, there will also be further optimizations and additions to the Avista software, such as in the area of warehouse management. This is being done in close cooperation with Avista.
AI (artificial intelligence) will also be a topic for the ERP system in the near future, as it is for the entire LQ Group. The first concrete considerations regarding the use of AI in production, for example in final inspection, have already been made. Further considerations, such as the use of generative AI in various areas of the company, are planned for the second half of 2024.