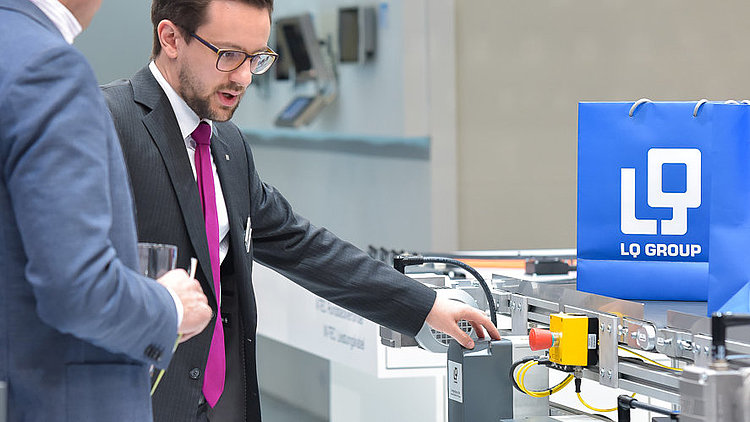
LQ makes every effort to complete every order on time
The global economy is currently facing a massive resource problem: many raw materials are becoming rare. This is currently a concern not only for the mechanical engineering sector, but for the entire economy. The Corona pandemic has led to an unprecedented economic slump. Now that the worst seems to be over, the signs are pointing to reconstruction and recovery. But the current shortage of raw materials is currently putting a damper on the recovery.
Almost all industries are directly or indirectly affected by enormous price increases, supply bottlenecks and shortages of raw materials. Long delivery times are the consequence and have to be accepted. In some cases, components have to be completely dispensed with. Materials such as plastic or copper in particular are in high demand and difficult to find on the market. At the same time, Europe is dealing with 13 force majeures, 11 plant breakdowns, 22 slowdowns and 24 maintenance shutdowns in plastics production (as of mid-April 2021). This is compounded by lower imports from Asia, the Middle East and the US. The reason is that demand is outpacing supply in these traditional export countries as well. Therefore, LQ Group is not spared from the present situation either.
"In the current situation, good planning and forward-looking action are essential. The order situation is positive and almost back to pre-pandemic levels. Our optimized warehousing and detailed planning help us to process as many orders as possible on time," says Friedrich P. Link, Managing Director of LQ Mechatronik-Systeme GmbH in Besigheim. "Should there nevertheless be delays or cancellations, we ask our customers for their understanding for this special situation. At LQ, however, we will do everything in our ability to ensure that this case does not occur," he continued.
The situation is serious but not hopeless. Experts predict an improvement by the end of the fourth quarter of 2021, by which time at the latest supply chains should be running smoothly again and the market should gradually return to normal. Until then, we as a system supplier are dependent on even closer cooperation with our customers and suppliers and on figures from both that are as reliable as possible in order to be able to deliver on time. Only with one another and with a certain flexibility in terms of the materials used can we achieve our common goal of supplying the end customer as requested during this period.
Decentralization and modularization as the future in mechanical and plant engineering
Modularization brings many advantages for machine and plant engineering. For example, modular control cabinets can minimize the variety of parts, costs, installation and machine downtimes, and increase efficiency. But not only in the control cabinet but also at the field level, decentralized modules can awaken considerable potential. LQ Group has specialized in offering customer-specific solutions for both approaches.
If a machine fails during operation, it is necessary to react quickly in order to avoid delays in production and high costs. However, the search for the fault often turns out to be a long process because each component has to be examined individually. The formation of function modules has many advantages: The customer benefits from significantly lower machine downtimes and can save huge costs that would have been incurred in the event of a prolonged downtime. Unlike conventional control cabinets, each module in the modular control cabinet contains a defined input, output and software interface. Thanks to separable connections, the modules can be replaced quickly and easily - a service that pays off.
Using the plug & play principle, the prefabricated and fully function-tested modules can be installed directly on site. Simply hook them up, connect them - and you're done. With the concept of the modular control cabinet, LQ has shown that downtime can be reduced to a minimum and that costs, variety of parts and procurement effort can be minimized many times over. Function modules from LQ can be installed not only centrally in the control cabinet, but also decentrally at the consumer. Each module acts autonomously and supplies data to neighboring modules or the central control system. Efficiently automated machines and systems minimize costs and ensure product quality. Modularization can be described very clearly as the future of mechanical and plant engineering.
However, there is no universal answer to the question of centralized or decentralized. Often, the combination of elements from both approaches is the most efficient solution. Here, it always depends on the requirements and the tasks to be performed. With the function modules from LQ, customers benefit from a wide range of products for both the control cabinet and the field level. This covers a wide range of application areas and can even make a central solution superfluous in many cases. In each case, LQ offers customized and customer-specific solutions and can help to increase the functionality in the field level of the customers and reduce the wiring effort at the same time.