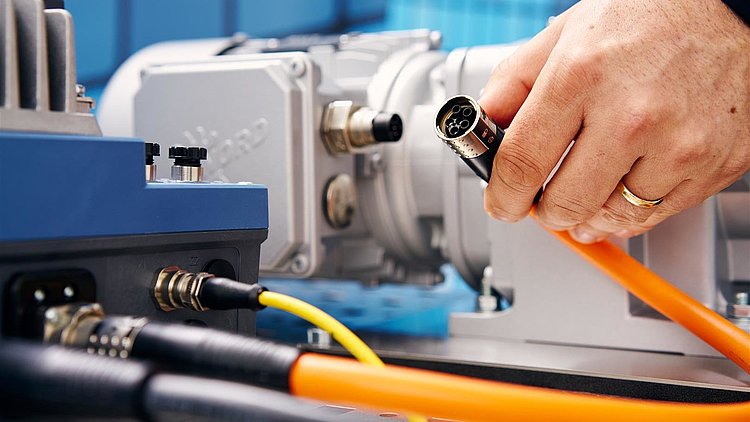
Making asynchronous motors more efficient with frequency inverter
Asynchronous motors can be found as drives in many different applications, whether pumps, fans, electric vehicles or machine tools, it is impossible to imagine today's industry without them. Unfortunately, asynchronous motors with their constant speed are not very efficient. Legal requirements and the economic necessity of energy efficiency have caused a rethink.
In order to achieve the minimum efficiencies, changes to existing motor technologies are often necessary. Usually, this leads to the use of more sheet metal and copper. However, it is often worthwhile to revise and optimize older concepts. Here, so-called frequency converters are attracting more and more attention. The main task of a frequency converter is to convert the uniform AC voltage from the power grid into an AC voltage whose amplitude and frequency can be changed. By controlling the frequency and voltage, it is possible to continuously regulate the speed or torque of the three-phase motor. In addition, a frequency converter can be used to directly change the direction of rotation. Typical applications for frequency converters are speed controllable milling spindles for CNC machines.
Frequency inverters cut energy requirements in half
Depending on the application, energy costs can often be halved. For pumps and fans, frequency inverters are even the better choice instead of mechanical control concepts, since in many applications very high energy losses occur due to so-called throttle control. Constant-speed drives always provide the maximum required flow rate, which is adjusted to the demand via valves. In this process, the excess energy is destroyed to a certain extent. It makes more sense to use a frequency converter to adjust the motor speed to the flow rate that is actually required at the moment. In this way, variable-speed operation can achieve energy savings of 50 %, and in some cases even up to 70 %.
Optimally connected at all times with W-TEC power cables
Now there is the question of the optimal connection between control, frequency converter and motor. This is where our W-TEC power cables come into play. In combination with the X-TEC circular connector, they form the perfect connection for asynchronous motors and frequency inverters up to 400 V. With our large selection of different designs, we have the right solution for almost every application. Whether shielded, unshielded, angled or straight - our W-TEC power cables are ideal for connecting asynchronous and three-phase motors up to 7.5 kW as well as frequency converters. Even in extremely confined spaces, systems can be easily connected with our W-TEC power cables. In addition, pluggable solutions can be serviced, replaced and put back into operation more quickly in an emergency. This not only increases efficiency, but also reduces costs in the long term. The figures speak for themselves. The energy-saving potential exists throughout industry and is waiting to be exploited. You can find out more about our W-TEC power cables here.